Messlösungen im Vergleich
Wenn es um die Messung von Distanzen oder komplexeren Objektgeometrien im industriellen Kontext geht, gibt es keine Universallösung. Je nach konkreter Messaufgabe und Anforderung stehen verschiedene Methoden zur Wahl.
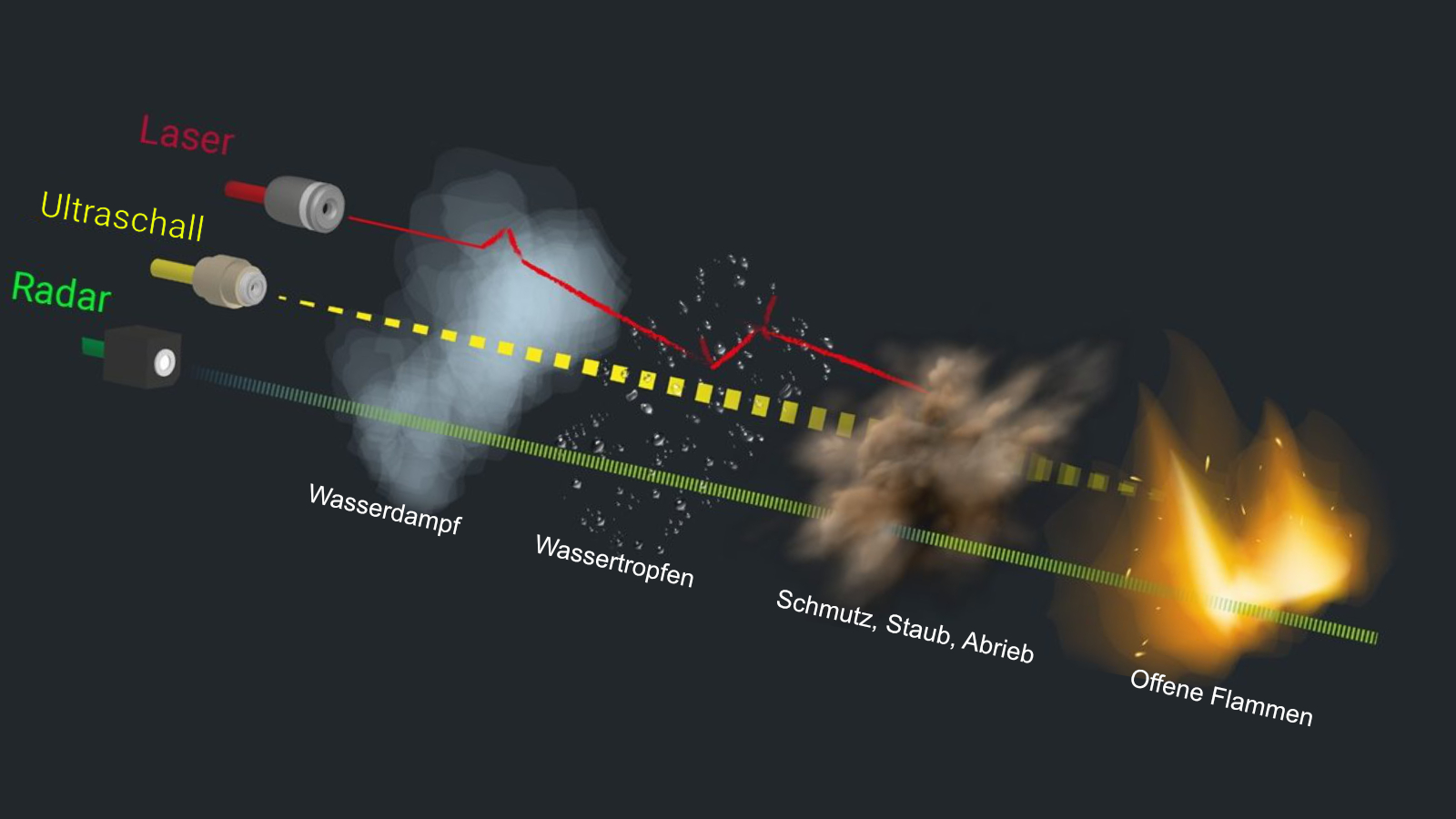
Wenn es um die Messung von Distanzen oder – noch komplexer – um die Bestimmung von Objektmaßen in industriellen Kontexten geht, stehen verschiedene Messlösungen zur Verfügung. Je nach spezifischer Messaufgabe und Anforderungen eignen sie sich mehr oder weniger.
Bei mecorad verstehen wir die einzigartigen und komplexen Herausforderungen bei der Verarbeitung von heißem Stahl und Metall. Sowohl die vorgelagerte als auch die nachgelagerte Verarbeitung in solchen Umgebungen ist nicht nur anspruchsvoll, sondern erfordert auch maßgeschneiderte Lösungen. Daher können die folgenden Schlüsselfragen bei der Auswahl der richtigen Messlösung helfen:
- Welche Genauigkeit wird benötigt?
- Welche Umgebungsbedingungen herrschen? (z. B. Staub, Dampf, Hitze oder sogar Vakuum).
- Weist das Material spezifische Eigenschaften auf?
Dieser Artikel konzentriert sich auf den Vergleich der berührungslosen Messmethoden: Laser, Ultraschall und Radar. Diese Technologien werden häufig verwendet und sind oft eine bevorzugte Alternative zu isotopischen Lösungen wie Röntgenstrahlen. Im Gegensatz zu Röntgenstrahlen stellen sie keine radioaktive Gefahr für Arbeiter oder Arbeitsplätze dar und sind daher deutlich sicherer.
Ultraschallbasierte Messlösungen
Funktionsweise
Ultraschallsensoren messen Entfernungen mithilfe des Laufzeitprinzips. Dabei sendet der Sensor hochfrequente Schallwellen im Bereich von 20 kHz bis 1 GHz aus, die sich in der Luft ausbreiten. Sobald diese Wellen auf ein metallisches Objekt treffen, werden sie reflektiert und zum Sensor zurückgesendet. Durch die Berechnung der Zeitverschiebung des zurückkehrenden Signals wird die Entfernung präzise ermittelt.
Vorteile
- Effektiv bei komplexen oder transparenten Objekten.
- Geeignet für glänzende oder homogene Materialien.
- Häufig in der Qualitätskontrolle eingesetzt, um Materialfehler, Einschlüsse oder Verunreinigungen zu erkennen.
Einschränkungen in der Industrie
- Störfaktoren aus der Umgebung:
In instabilen Temperaturverhältnissen oder bei sich ändernder Luftzusammensetzung können die Schallwellen an Präzision verlieren. - Herausforderungen bei staubigen oder dampfigen Umgebungen:
- Staub oder Mikro-Wassertropfen streuen die Ultraschallwellen und stören die Signalübertragung und -reflexion.
- Glühende Stahlplatten erzeugen Wärmekonvektionen, die die Ultraschallsignale ebenfalls stören.
Laserbasierte Messlösungen
Funktionsweise
Ein Laser (Light Amplification by Stimulated Emission of Radiation) nutzt elektromagnetische Wellen, die sich mit Lichtgeschwindigkeit bewegen. In industriellen Anwendungen basieren Lasermessungen auf Triangulation, Phasenverschiebung oder Laufzeitmessung.
Vorteile
- Sehr präzise unter idealen Bedingungen.
- Geeignet für Objekterkennung und Geschwindigkeitsmessung.
Herausforderungen unter schwierigen Bedingungen
- Staub und Ablagerungen:
Staub oder Ablagerungen blockieren den Laserstrahl und erfordern häufige Reinigung – eine Aufgabe, die in der Industrie oft unpraktisch ist. - Glühende Objekte und offene Flammen:
Standard-Rotlichtlaser sind bei glühendem Metall aufgrund der ähnlichen Infrarotfrequenzen ineffektiv.- Lösung: Blaulichtlaser können dieses Problem lösen, sind jedoch teuer und nicht für alle Aufgaben geeignet.
- Nasse oder reflektierende Oberflächen:
- Variierende Reflexionseigenschaften beeinträchtigen die Messgenauigkeit.
- Große Wassertropfen, wie sie in der Schlackewäsche der Stahlindustrie vorkommen, brechen den Laserstrahl.
- Eine konstante Distanz zwischen Sensor und Objekt ist entscheidend für stabile Signale.
Radarbasierte Messunglösungen
Funktionsweise
Die Radarmessung basiert auf elektromagnetischen Wellen. Der Sensor sendet hochfrequente Signale aus, die sich mit Lichtgeschwindigkeit ausbreiten. Die Entfernung wird berechnet, indem das reflektierte Signal des Objekts gemessen wird.
Vorteile
- Resistent gegenüber Umwelteinflüssen:
Radar bleibt auch in staubigen, feuchten oder heißen Umgebungen präzise. - Durchdringt Nebel, Dampf und Flammen:
Im Gegensatz zu Laser ist Radar nahezu unempfindlich gegenüber visuellen Hindernissen. - Zuverlässig in dynamischen Umgebungen:
Der fokussierte Radarstrahl gewährleistet Messungen, selbst wenn Hindernisse teilweise die Sichtlinie blockieren.
Warum Radar ideal für die Verarbeitung heißer Metalle ist
Im Vergleich zu Laser ist Radar in Laborumgebungen möglicherweise etwas weniger präzise. Unter industriellen Bedingungen bietet es jedoch eine unvergleichliche Robustheit und Zuverlässigkeit. Daher eignet es sich hervorragend zur Messung von Breite, Dicke und Länge von heißem Metall.
Fazit: Die richtige Technologieauswahl ist entscheidend
Die Auswahl der passenden Messtechnologie hängt von den Umgebungsbedingungen und der benötigten Genauigkeit ab. Während Ultraschall und Laser in kontrollierten Umgebungen hervorragende Ergebnisse liefern, ist Radar in rauen industriellen Umgebungen unschlagbar.
Bei mecorad integrieren wir Radar in unsere IIoT-Messlösungen. So garantieren wir präzise Ergebnisse selbst unter härtesten Bedingungen.
Kontaktieren Sie uns, um zu erfahren, wie unsere innovativen Lösungen auch Ihre Prozesse optimieren können.