Measurement options for hot metals forming
When it comes to the measurement of distances or -even more complex- object dimensions in industrial contexts, there is no one and only right solution. Various methods are available, depending on the specific measuring task and requirements.
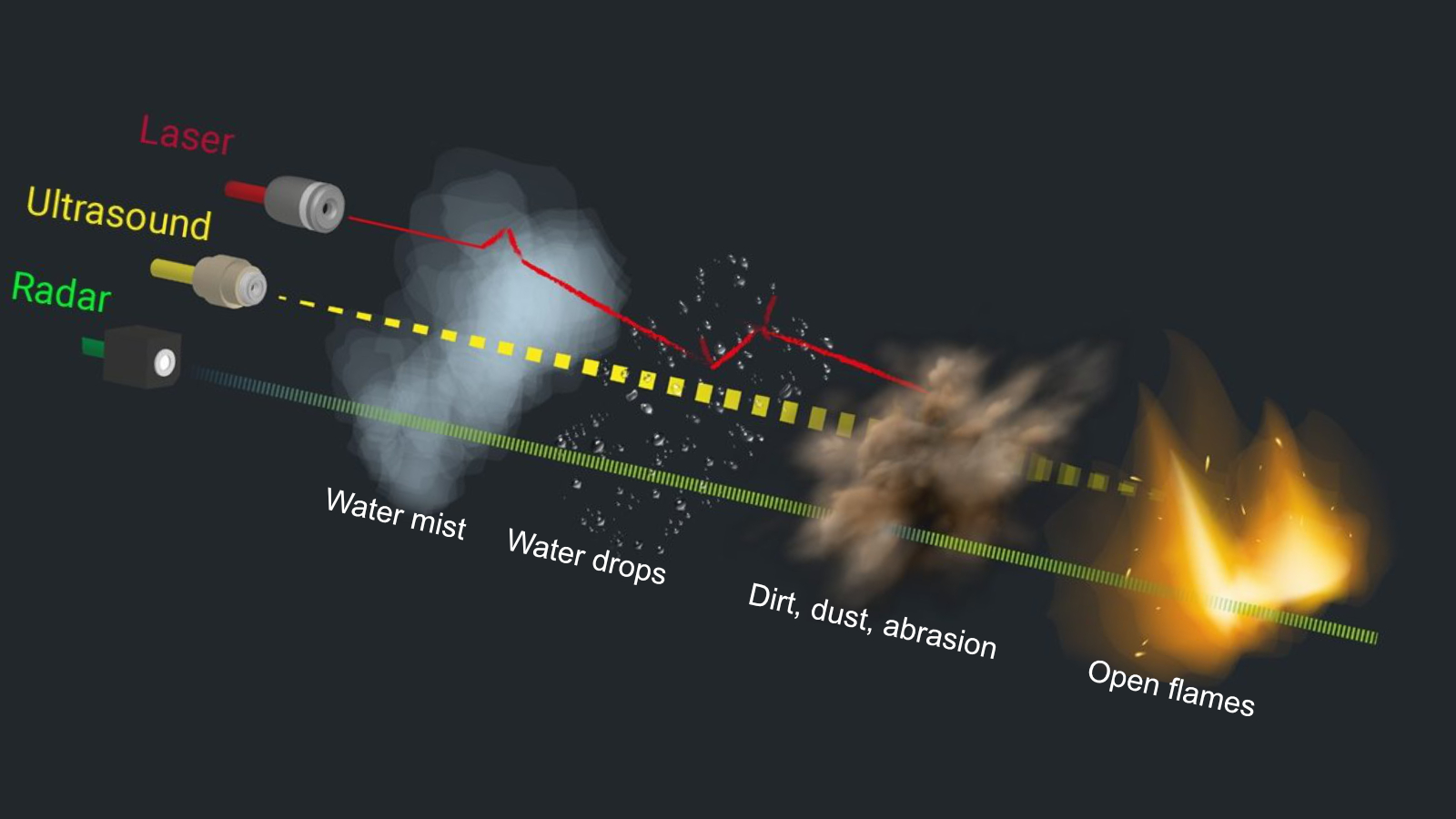
For measurements in hot metals forming, there are several options.
At mecorad, we fully understand the unique and complex challenges involved in processing hot steel and metal. Both upstream and downstream processing in such environments are not only demanding but also require tailored solutions. Therefore, the following key considerations can help guide you in selecting the right measurement solution:
- What level of accuracy is required?
- What are the environmental conditions? (e.g., dust, steam, heat, or even a vacuum).
- Are there any specific characteristics of the material?
This article focuses on comparing the contactless measurement methods of laser, ultrasound, and radar. Since these technologies are widely used, they are often preferred over isotopic solutions like X-rays. Unlike X-rays, they do not pose radioactive hazards, making them a much safer alternative.
Measurement with Ultrasound
How It Works:
Ultrasound sensors measure distances by using the time-of-flight principle. In this process, the sensor emits high-frequency sound waves ranging from 20 kHz to 1 GHz, which then travel through the air. When these waves encounter a metallic object, they are reflected back toward the sensor. By calculating the time shift of the returning signal, the distance is accurately determined.
Advantages:
- Effective for complex or transparent objects.
- Works well with shiny or homogeneous materials.
- Commonly used in quality control to detect material defects, inclusions, or impurities.
Limitations in Industrial Settings:
- Interference from the environment: In unstable temperatures or changing air compositions, sound waves can lose accuracy.
- Challenges with dusty or steamy environments:
- Dust or micro water droplets scatter the ultrasound waves, interrupting signal transmission and reflection.
- Heat convection around glowing steel slabs disrupts the signal.
Laser measurement
How It Works:
A laser, which stands for Light Amplification by Stimulated Emission of Radiation, uses electromagnetic waves that travel at the speed of light. In industrial applications, lasers usually rely on one of three principles: triangulation, phase shift, or time-of-flight. Each method has its own advantages depending on the specific use case.
Advantages:
- Highly precise under ideal conditions.
- Suitable for object detection and speed measurement.
Challenges in Harsh Conditions:
- Dust and Deposits:
Dust or deposits block the laser beam, requiring frequent cleaning—a task often impractical in industrial settings. - Glowing Objects and Open Flames:
Standard red-light lasers are ineffective with glowing metal due to the similarity in infrared frequencies.- Solution: Blue-light lasers can mitigate this issue but are expensive and not suitable for all tasks.
- Solution: Blue-light lasers can mitigate this issue but are expensive and not suitable for all tasks.
- Wet or Reflective Surfaces:
- Surfaces with varying reflective properties reduce accuracy.
- Large water droplets, such as those in steel cinder washes, refract laser signals.
- Maintaining a consistent sensor-to-object distance is essential for robust signals.
Radar measurement
How It Works:
Radar measurement relies on electromagnetic waves. High-frequency signals are emitted, traveling at the speed of light. The sensor calculates distance by measuring the reflected signal.
Advantages:
- Resistant to environmental interference: Radar remains accurate in dusty, wet, or high-temperature environments.
- Penetrates fog, steam, and flames: Unlike laser, radar waves are largely unaffected by visual obstructions.
- Reliable in dynamic settings: The focused radar beam ensures measurements are not hindered by partial obstructions.
Why Radar is Ideal for Hot Metal Processing:
Radar may be slightly less precise than lasers in laboratory conditions. However, it excels in industrial environments where precision is required despite harsh conditions. This makes it the best choice for measuring width, thickness, and length of hot metal.
Conclusion: Choosing the right technology
Selecting the right measurement technology depends on environmental conditions and the required accuracy. While ultrasound and laser excel in controlled settings, radar is unmatched in robustness and reliability under industrial conditions.
At mecorad, we integrate radar into our IIoT measurement solutions. This ensures precise results even in the harshest environments.
Contact us to learn how our innovative solutions can benefit your operations.