The Doppler Effect describes the change in frequency or wavelength of a wave in relation to an observer moving relative to the source of the wave. One of the most significant applications of the Doppler Effect is in Doppler radar technology. Doppler radar detects motion by measuring the frequency shift of returning radar signals, which is crucial for accurate speed measurement and weather forecasting. This technology has been instrumental in advancing meteorology, enabling precise tracking of storm systems and providing early warnings for severe weather events.
First Experiments with Doppler Effect
The development of radar technology dates back to the early 20th century. Initial radar systems could only detect the presence and distance of objects. However, integrating the Doppler Effect allowed for the detection of object velocity, vastly improving radar capabilities.
Christian Doppler first presented his principle in 1842 in his paper titled “On the Colored Light of the Double Stars and Certain Other Stars of the Heavens.” His work initially focused on the frequency changes in sound waves, but the principles he described were later found to apply to all types of waves, including light and radio waves.
The Doppler Effect was experimentally confirmed in 1845 by the Dutch scientist Christophorus Buys Ballot. Using a group of musicians playing trumpets on a moving train, Buys Ballot demonstrated the change in pitch predicted by Doppler. This experiment was one of the earliest confirmations of Doppler’s theory.
In the early 20th century, the application of the Doppler Effect expanded significantly. French physicist Henri Becquerel used the Doppler Effect to study gamma rays, and the development of radio technology paved the way for Doppler radar. By World War II, radar technology had become sophisticated enough to incorporate Doppler shifts, allowing for more accurate detection and tracking of moving objects.
Speed Measurement with Doppler Radar
One of the remarkable capabilities enabled by the Doppler Effect in radar technology is precise speed measurement of moving objects. Doppler radar calculates the velocity of an object by analyzing the frequency shift between the emitted and received radar signals. If a radar system emits a signal at 100 MHz and receives a reflected signal at 101 MHz, it indicates that the target is moving towards the radar at a speed that causes this frequency shift.
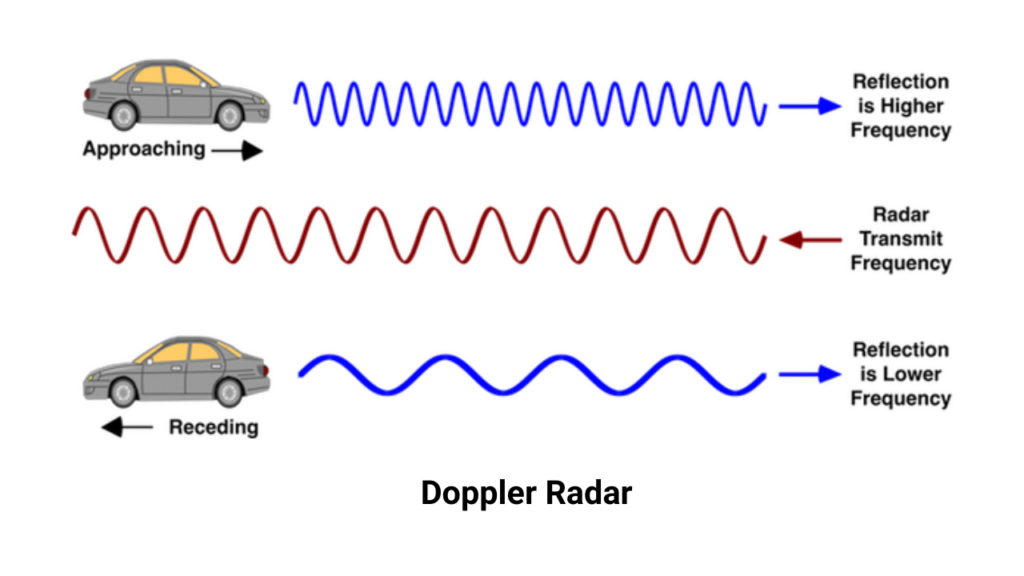
Applications in Law Enforcement and Traffic Control
Doppler radar is widely used in law enforcement for speed enforcement. Police radar guns measure the speed of vehicles by detecting the Doppler shift in radar waves bounced off moving vehicles. This technology allows police officers to accurately determine if a vehicle is exceeding the speed limit.
Aerospace Applications
In aviation, Doppler radar is used to measure the ground speed of aircraft. By analyzing the frequency shift of radar signals bounced off the ground, aircraft speed relative to the ground can be accurately determined, aiding in navigation and flight control.
Radar and the Doppler Effect
As the radar source moves towards a target, the radar waves become compressed, resulting in an increase in frequency. Conversely, when the radar source moves away from the target, the radar waves are stretched, leading to a decrease in frequency. This change in frequency due to motion is the essence of the Doppler Effect and is crucial in detecting and measuring the speed of objects using radar technology.
Future Directions and Innovations
The Doppler Effect continues to inspire innovations in radar technology. Ongoing research aims to enhance radar systems’ sensitivity and accuracy, particularly in adverse weather conditions and complex terrain. Advances in signal processing and radar engineering promise to further refine Doppler radar applications across various industries, from automotive safety systems to aerospace navigation.
The Doppler Effect’s impact on radar technology underscores its significance in modern science and industry. From meteorology to military applications, this fundamental principle continues to shape our understanding of waves and their interaction with moving objects, driving technological advancements.
Learn more about our Scout Sensor Series.